How to Stop Leaks Fast with Injection Grouting
- BRT
- Feb 1, 2023
- 3 min read
Updated: Oct 8, 2024
Imagine this: you’re a property manager overseeing the construction of a new fitness facility in the basement of one of your buildings. You found a great contractor, approved the design and budget, and are eager to get started.
But there’s one problem. You’re standing in a pool of water where that new gym is supposed to go.
What’s your next step?
Spoiler: call us!
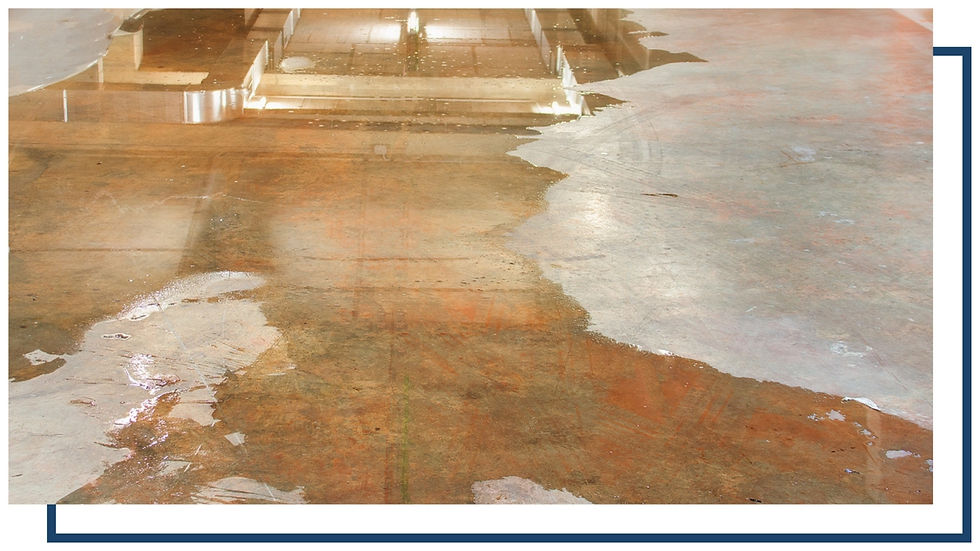
Situations like this are becoming more commonplace in many urban markets, including New York City. As real estate prices continue to rise, building owners, developers, and property managers are refurbishing their unused below-grade spaces in an effort to increase their building’s usable square footage.
In theory, this sounds like a pretty solid plan. After all, it allows you to transform those barely-used basements and old boiler rooms into beautiful, functional spaces. But in many buildings (especially older ones), those below-grade areas weren’t originally designed as usable spaces and therefore weren’t waterproofed properly—or at all.
This poses a unique challenge because, in high-density urban areas like New York City, most building owners don’t have the option to excavate their building’s foundation in order to apply a new waterproofing membrane to the exterior. In situations where this is possible, shoring and lagging costs often make the project cost-prohibitive.
Luckily, there’s an easier, faster, and more cost-effective way to make your space watertight: injection grouting.
What is injection grouting?
Injection grouting is a process of filling cracks and voids in concrete and masonry surfaces as a means of stopping leaks. Through a series of drilled holes, chemical grout is injected (pumped) into the surface via packers, plugging the holes and making the area watertight.
Unlike cementitious grout used for block filling, chemical grout is more viscous, which allows it to travel anywhere water can go. Engineered for use in wet environments, chemical grout swells and solidifies when it comes into contact with water, creating an impermeable barrier that blocks the flow of water immediately.
Injection grouting offers long-term waterproofing protection and can be used when:
You have active leaks below-grade (e.g., in foundations, basements, tunnels, vaults, parking garages)
Excavation isn’t possible
You want to avoid the expense of shoring and lagging
You don’t have active leaks but want to take preventative measures to ensure your area is watertight
Here’s how it works.

Crack Injection & Joint Injection
For leaking cracks in walls, slabs, wall slab connections and cold joints

The most popular injection grouting method is crack injection. Crack injection is used when the source of leaks in below-grade structures is identified as a crack in a wall or slab. As the name implies, crack injection pumps grout into the cracks, stopping the flow of water at the source.
Joint injection is similar and is used when water penetration occurs at wall slab connections and cold joints. Leaks in these areas are usually seen in newer buildings where waterstops and waterproofing are failing or are improperly installed. In these situations, resin can be injected into the joints to create a watertight seal.
Curtain Grouting
For rubble walls or systemic waterproofing failures

If your building has multiple leaks, a masonry foundation, or no waterproofing, curtain grouting is your best bet for leak remediation.
Whereas crack/joint injection delivers a more targeted solution, curtain grouting allows you to stop (and prevent) multiple leaks simultaneously. Holes are drilled in a large grid pattern before the grout is pumped and fills the entire back surface of the wall.
This technique is ideal for masonry and rubble wall foundations where it’s often challenging to isolate and stop a single leak.
Soil Grouting
To stabilize soils and eliminate the need for costly dewatering

New buildings built on contaminated soil come with hefty soil remediation costs, and the combination of contaminated soil and high water pressure can be expensive for developers. You can eliminate these costs and avoid dewatering by using soil grout to solidify and stabilize poor soil conditions.
Soil grout can also be used as underpinning or in coordination with underpinning in core and shell projects that involve lowering basement elevations. One key advantage is that you don’t need to disturb or touch party (shared) walls.
Ready to stop leaks fast?
Contact us! Every situation presents unique complexities, and we’re here to help.
We can also partner with your waterproofing consultant, architect, or other design professional to determine the best solution for your specific problem.
With our extensive grouting knowledge and deep expertise, we help clients choose the right product, application, and contractor to get the job done right.